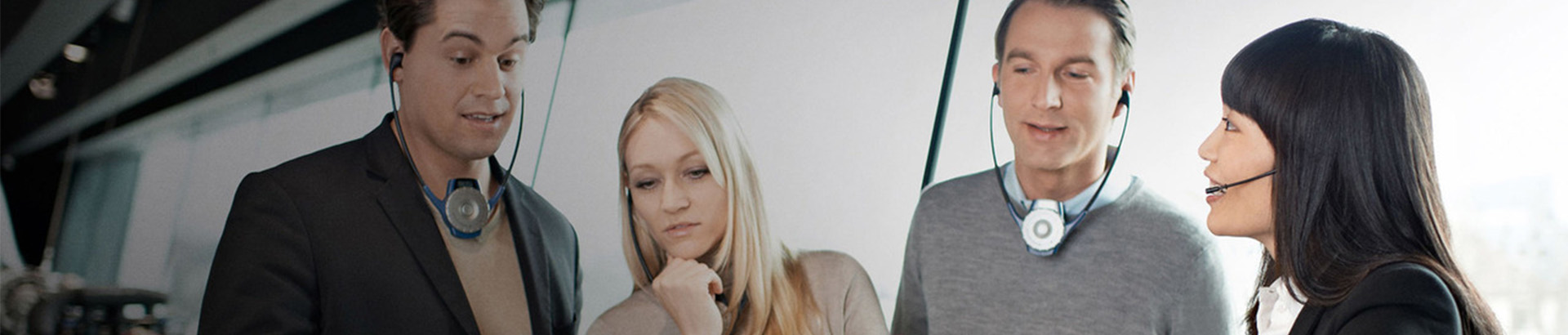
Your Location : Home / News Center >> Industry News >> Matt black wall hung toilet manufacturer process
NEWS CENTER
Matt black wall hung toilet manufacturer process
Release time:2020-03-28 Hits: 【Print】

1) Raw materials for ceramic production
It is divided into porcelain clay and glaze. The raw materials are basically the same, but the ratio of raw materials is different.
Its main ingredients: Feldspar, quartz, iron oxide, zirconia, aluminum powder, magnesium oxide, pigment.
K2O SiO2 ZnO ZrO2 AL2O3 MgO
Clay: clay used to produce pottery and porcelain.
Porcelain: the finished product that is completely vitrified into porcelain during high temperature firing.
Pottery: the finished product that is not completely vitrified and cannot be made into porcelain in high temperature firing.
Difference between porcelain and pottery: raw material formula, product water absorption, firing temperature.
Slurry: the raw material used for forming grouting.
Glaze: the raw material used for semi-finished glaze spraying.
Production process: ball milling, screening, iron removal, pool storage.
Ball milling and sieving must reach 325 national standards.
2) mold
Gypsum mould used for forming grouting.
Material: gypsum powder
Features: fast water absorption, short setting time, convenient repair and low price.
Grouting times: 80 times - 120 times.
Production process: 3D drawing design, original mold artificial sculpture, master mold made of resin.
After forming the master mold, the sub mold is produced through the master mold for forming grouting.
3) Injection molding
The slurry is used to form the semi-finished body in the gypsum mold.
At least two modular models are combined for each molding product.
Molding method: single side suction, double side suction.
Production process: grouting, grouting, demoulding, splicing and drilling, trimming.
4) spray glaze
The glaze is evenly sprayed on the semi-finished product body.
Spraying method: manual spraying and manual spraying.
5) firing
The semi-finished product sprayed into glaze is the product formed after being heated at high temperature in the kiln.
Firing shrinkage: no more than 1.15
Firing time: 13-15 hours.
Firing temperature: 1210 ℃ -- 1290 ℃
Firing process: pre tropical zone, firing zone, cooling zone.
Kiln type: shuttle kiln, tunnel kiln, roller kiln.
Six
6) test
Size: fineness, specific gravity (moisture content), shrinkage, strength, bending resistance, flow thixotropy.
Glaze: flow, thixotropy, fineness, specific gravity, color difference, high temperature flow, drying time, adaptability of green glaze (in order to control thermal stability).
Color difference: compared with Kohler standard color plate in the United States, imported color difference meter is used for tile production and firing.
Color: visual inspection.